- Quality Control
Incoming Inspection Service
Incoming Inspection Service
Incoming inspection is one of the most effective quality control services, established to inspect all shipments of goods from suppliers to detect material failures prior to entering the warehouse and production line areas.
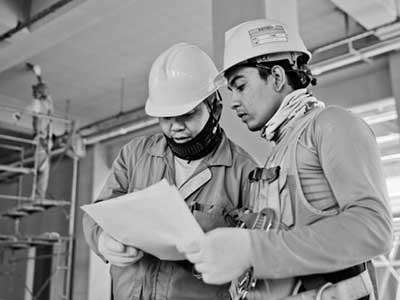
How does the Incoming Inspection service help my company?
The objective of the Incoming Inspection service is to validate the conformity of a batch of parts, materials or products based on their quality standard,ensuring that the parts entering the plant have the expected quality to start the manufacturing process.
Top 4 benefits of Incoming Inspection
The Incoming Inspection or Incoming Quality Control service allows you to verify the quality parameters of materials, parts or products coming from your suppliers, which is why Plant Managers, Quality Managers and Quality Assurance Managers in Mexico and USA, decide to hire the Incoming Inspection service from A&T Sorting Company, achieving a superior quality in their manufacturing.
- 1. A&T Sorting Company´s Incoming Inspection or Incoming Quality Control Inspection service helps you to select the best suppliers. Remember that the first way to limit defects in your products is to prevent them from occurring.
- 2. Introducing A&T Sorting Company´s incoming Inspection avoids wasted materials, empty warehouses, which saves you money.
- 3. Implementing A&T Sorting Company´s Incoming Inspection or Incoming Quality Control helps improve your relationship with your customers by preventing non-quality costs, product losses, charges and claims, since your company will have the high quality materials it needs for its production.
- 4. A&T Sorting Company's Incoming Inspection service will allow your customers to receive their product on time: having certified materials prevents shipment delays and poor quality.
How do I know if I need Incoming Inspection service?
If you have suppliers in development or suppliers with low quality assurance that are sending a large amount of materials with defects to your plant and this in turn is translating into quality problems for your customer, it is necessary to look for an Incoming Inspection service.
How to choose the Incoming Inspection provider or company?
There are several people who can be involved in the selection of the Incoming Inspection provider. Read the full post here
What to consider when quoting the Incoming Inspection service?
The cost of the Incoming Inspection service varies significantly depending on the requirements of each company. To quote this service you must have the following information:
- Project Duration: Tell us if your project is temporary or fixed. Specify the number of hours,days or months.
- Type of service required: Tell us the type of project, for example: visual inspection, inspection with measuring equipment, draw, cs1, cs2, gp12, residences or representations.
- Number of Inspectors: How many inspectors (specify how many inspectors per inning).
- Work Schedules: Indicate work schedules, shifts and days of work.
- Mention the quantity of parts to be inspected or certified.
- What PPE does the personnel require to enter your plant?
- Tools: If the inspection to be performed requires tools, please specify which ones and if they will be provided by you as a customer or if they are required by your draw supplier.
- Consumables: Detail the consumables the team will need for the inspection, e.g, water markers, oil markers, labels or others.